Round hole perforation
Strength, versatility and high open areas
Round hole perforations provide the possibility of a large open area, and geometrically, the round hole is the most stable shape.
Key benefits of round hole perforation
- Provide excellent strength and large open area for filtration, air flow, sound control, or material flow.
- Available in hole sizes from 0.3 mm.
- Available with hole arrangements in triangular, diagonal, straight, staggered, or decorative patterns.
- Suitable for various materials, meeting both technical and aesthetic requirements.
Applications examples
- Agriculture: Used in sieves for sorting and grading seeds, stones, and other materials.
- Recycling and bulk handling: Ideal for sorting bulk materials in the recycling operations.
- Building industry: Commonly applied in facades, offering aesthetic appeal and sun protection, as well as for balustrades or balconies as infill panels.
- Ventilation and safety: Used in protection and ventilation panels for machinery, IT equipment, doors, windows, and gates, providing safety with airflow.
- Acoustics: Offers sound absorption for acoustic applications, combining function with design flexibility.
Technical information - round hole perforation
Arrangement of holes
Round holes (R) with a 60° staggered triangular pitch (T) are the most common configuration, offering high mechanical strength and versatility in open areas. The equal spacing between holes of this arrangement maintains uniform strength, even with a reduced pitch.
Round holes (R) with a staggered pitch (Z) provide balanced open areas and structural stability. Ideal for applications requiring airflow and durability, the Z configuration combines flexibility and strength.
Round holes (R) with a 45° staggered pitch (M) also known as diagonal pitch offer unique design options and moderate open areas. This alignment adds visual appeal without sacrificing strength, perfect for aesthetics-focused applications.
Round holes (R) with a rectangular (U) pitch align in straight, uniform rows, creating a grid-like pattern with predictable strength and open areas. This layout suits applications needing controlled airflow or a structured, decorative appearance.
T = Triangular pitch
Z = Staggered pitch
M = Diagonal pitch
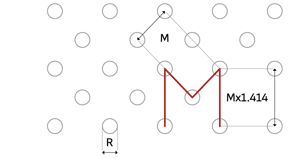
U = Rectangular pitch
Beginning and end of perforated areas
A closed end pattern involves special tooling to create a uniform edge at the start and end of the perforated area, giving a clean, continuous look ideal for decorative and architectural applications. This process is more costly and may extend production time.
A semi-closed end pattern balances cost-effectiveness and visual appeal, offering a partially finished edge that improves appearance without the full expense of a closed pattern. Suitable for applications needing a moderate level of refinement.
The open end pattern is the standard option, where the perforated area begins and ends with partial or irregular rows due to the stepped perforating process. This approach is efficient and economical, ideal for non-decorative applications or areas that will be framed. However, it may lack the finished look needed for visible applications.
Closed end pattern
Semi closed end pattern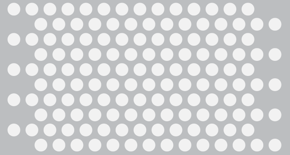
Open end pattern
Materials
Round hole perforation are available in various materials, including:
- Mild steel
- Stainless steel
- Galvanised steel
- Aluminium
- Brass
- Other alloys